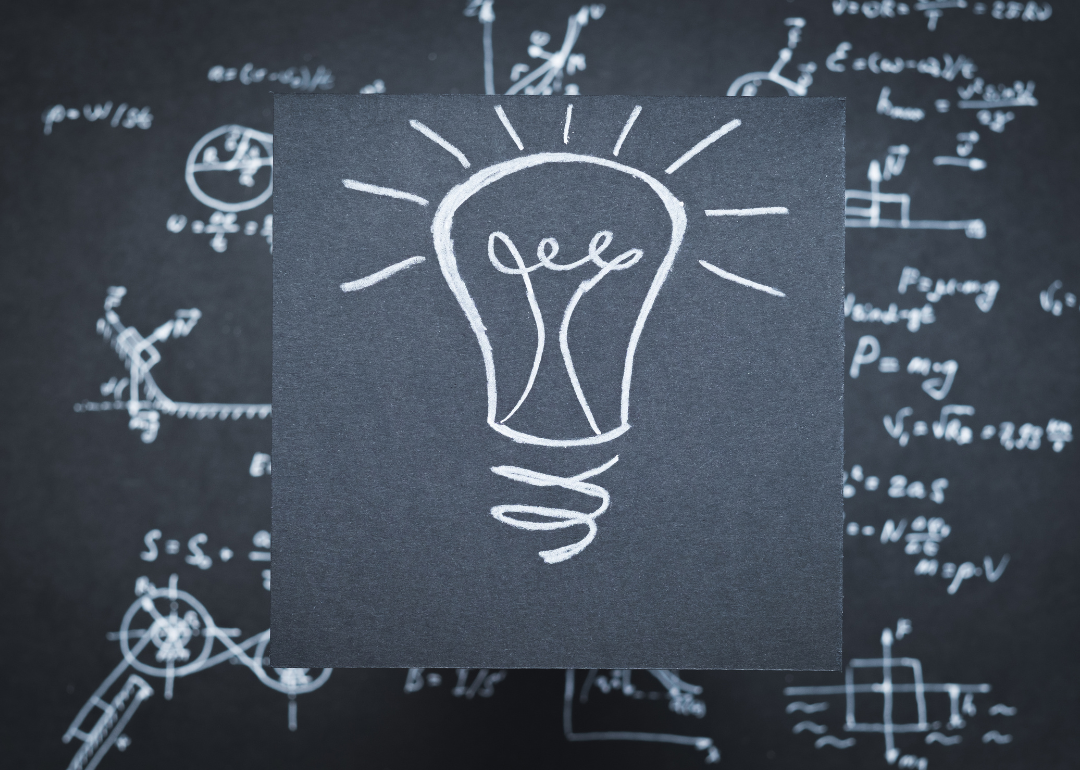
How 30 things are unexpectedly made
How 30 things are unexpectedly made
The average American in 2017 spent almost $10,000 on products ranging from meals to clothes.
Each person in that year averaged more than $7,000 on food, more than $1,000 on apparel and other services, and more than $700 on personal care products and services, according to the Bureau of Labor Statistics. That's thousands of purchased products, each of which was made through a distinctive manufacturing process. Amazon alone sells more than 500 billion goods on its website.
So where do the everyday products that Americans buy come from? To find out, Stacker consulted news articles, research papers, and one documentary television series to compile a list of everyday products created in surprising ways.
From chain links to jelly beans, read on to find out how unusual some of these production processes are—as well as the peculiar nature of some of the ingredients used.
Chain links
Chain links actually begin as a single, long, wire rod that is slowly narrowed and strengthened. The rod is then segmented and goes through a forming machine that bends the wire into its familiar, linked structure. The chain is next heated to 1,724 degrees Fahrenheit to harden the steel, then put into a cooling tank. These sudden, extreme temperature shifts actually change the molecular structure of the steel and harden it. The chain is then reheated to a lower temperature in order to get rid of the brittleness, and put into another container with cold water.
Toy dinosaurs
To make a plastic toy dinosaur, an original model is sketched before being sculpted in clay or wax, either by hand or printed out in a plastic 3D model. The completed primary model provides the basis for a silicone mold that is is then used for hard plastic molds. Next up are metal production molds, into which molten plastic is poured and cooled. When completely dry, the toy is hand-painted to create the final version sold in stores.
Jawbreakers
This popular candy, which is 90% sugar and includes ingredients like synthetic rubber, takes four days to create. Everything gets steamed and mixed for four hours straight at 300 degrees Fahrenheit, then set aside for 24 hours to cool in trays. Machines cut up the hardened mix and combine it with corn syrup to soften and sweeten it before adding natural and artificial flavoring along with icing sugar. Machines pull the thick goop into long ropes, then form them into balls that will serve as the gum centers of jawbreakers.
Jawbreakers with hard candy centers instead of gum undergo a different process of pressing candy powder into a solid, hard ball. Centers are poured hundreds at a time into a large spinning bowl called a coating pan. Here, water, corn syrup, food coloring, and powdered sugar are added 10 separate times for each of the layers of the jawbreaker. A full 24 hours later, the candy has dried and wax is added for a shiny finish.
Soap bars
Soap bars rely on a base of animal or vegetable fat mixed with sodium hydroxide for their consistency and cleaning properties. Ingredients are mixed together and boiled in a kettle, and sprayed in ribbons over trays to harden. The soap is then churned through augers, reshaped, and pressed through a “noodle plate,” creating pasta-shaped soap bits to further mix the ingredients together before dyes are added. Steel blades mix in the color to coat the soap noodles. Next fragrance is mixed in, the soap passes through another noodle plate, and finally through a forming plate that turns it into long bars. For the finishing touches the bars are cut down to size, stamped, and shaped before being wrapped and boxed.
Sewing needles
This everyday item starts out as thin, loose, and long rolls of steel wire. Through a two-day process, the wire is straightened, cut to size, and finally ground into a point by a large spinning wheel.
Crystal chandeliers
To make the crystal for chandeliers, silica sand, lead, hot ash, and other ingredients are loaded into a furnace and melted down. The resulting crystal is more sparkly and significantly stronger than glass. The crystal is then heated to 2,280 degrees Fahrenheit, and each individual piece is fused, molded, and bent into place with blow pipes and molds handled by experienced blowers. The process is difficult, time-consuming, and extremely dangerous. After the chandelier’s base is similarly made in a mold, all the parts are cooled in an oven and smoothed out with a blowtorch. Decorative details like 24-karat-gold leafing or paint is added, and the chandelier is put together by hand.
Wigs
A wig is another surprisingly dangerous product to make. To blend different shades and colors of hair together for highlights, wig artisans use a big comb with row after row of very sharp, steel barbs called a hackle. The hackle sits on a table with teeth pointed up while the wigmaker slides each shade of hair on to it in a pile. Then, he or she grabs one end of the hair and pulls it like a tail through the hackles repeatedly. If the artisan makes one wrong move while hackling in this way, he or she could pierce a hand or get badly scraped by the metal combs. With the hair blended, the artisan next spends more than 50 hours sewing the wig together strand by strand.
Rolling luggage
This widely used item starts out as thousands of small plastic pellets that are melted together and inserted into a luggage mold, which has a cooling system in it to harden the melted plastic in seconds. A robot moves the forms to another station, where workers attach handles, wheels, and other parts such as luggage feet. Wheels molded from nylon are coated in rubber and attached to the base along with an extendable handle.
Milk chocolate
Chocolate comes from cocoa beans, which are comprised of roughly 50% cocoa powder and 50% cocoa butter. To make chocolate, the beans are cracked open and separated from their shells before being broken down into nibs, refined, and melted. Sugar is added, the chocolate thickens, and is repeatedly mixed, flattened, reshaped, and aerated by machines. The reason people don’t see the cocoa butter in chocolate bars is due to a process called tempering, which is done to achieve a specific chemical makeup and texture. Mistempered chocolate can exhibit a white coating called a fat bloom. Additional flavors, from herbs to mushrooms, are added to the tempered chocolate in a holding tank before the chocolate is rolled out, dried and wrapped.
Pink erasers
Erasers are essential for almost anyone who has made a mistake while writing in pencil. But the synthetic rubber comprising the bulk of an eraser isn't what gives it the ability to erase. For that, vulcanized oil (vegetable oil treated with sulfur) is mixed in with the rubber to give it the power to break up and erase writing. Pink erasers have a number of additional ingredients, as well—from red coloring to accelerators. The mix is melted down, milled, hardened, and finally steam-pressed and cured at 325.4 degrees Fahrenheit. The rubber goes through a cold-water bath and is then cut and chopped to size before being tossed into a giant tank with some talc and spun for hours to soften the edges for the finished product.
Rubber bands
The process for creating rubber bands starts by machine-kneading a giant tank of rubber so it heats up and softens into a dough-like form. A mechanized rolling pin flattens the dough out before it is treated with sulfur and other chemicals to strengthen the rubber and make it more elastic. The product is shaped into long tubes that are heated for strengthening and finally sized and cut into the bands that have become so familiar. These machines are so efficient, they can cut 500,000 rubber bands an hour.
MLB baseballs
Professional-grade baseballs take a week to make. At the center of the ball is a round cork called the pill. The pill is encased in rubber, coated with liquid adhesive, and wound in four-ply wool. Three-ply yarn wraps the ball next, followed by a different, lighter three-ply wool. The last wrapping utilizes a very thin, poly-wool blend. With the ball’s center complete, it is coated with more liquid adhesive. A machine presses and cuts leather shapes with holes for stitching. Two pieces of leather make up the outside of the baseball, which is hand-sewn with 108 stitches.
iPads
This Apple product is too complex for machines to handle from start to finish, so each one is mostly made by hand. The workers who manufacture iPads have to wear static-proof, full-body jackets and take multiple “air showers” because any dust can destroy a full line of the machines. There are about 141 steps that go into each iPad—which takes five days and about 325 people to complete.
Jelly beans
The base of all jelly beans starts with what is called “slurry”: a mix of heated cornstarch, sugar, water, and corn syrup. The slurry gets inserted into a machine called a mogul that houses more than 1,000 molds giving the jelly beans their shape. The shell and shiny surface of each bean is created from beeswax and shellac. The shellac is derived from secretions of the female Kerria lacca, an insect native to Thailand.
Hourglasses
The hourglass gets its famous shape by being hand-blown, spun and shaped by machine, or through the joining of two pieces of lightbulb blanks. Sand (or beads, crushed marble, or other materials) are then poured through a hole in the top of the vessel. Before the hole is sealed and the glass fitted into a frame, the instrument must be tested and fine-tuned to ensure its accuracy. Sand is added and timed as it flows through the hourglass until the prescribed time period is over. That can be an hour, 30 minutes, or—most commonly for today's souvenirs—three minutes.
Lava lamps
To make a lava lamp, two metal coils—turned on when the lamp is activated—are put at the bottom of pre-shaped glass. This glass gets churned out by eight mechanized glass-blowers at a rate of 6,000 an hour. The “lava” is actually colored wax. A mix of chemicals, water, and dyes are added to make the wax denser than the liquid when cold, but less dense when heated. With the coils on, the wax floats to the top. The floating blobs cool and sink back down to the bottom, where they are reheated and rise again. This creates the lava lamp effect that became a psychedelic icon of the 1960s and is still popular more than half a century later.
Fake food for television
Not all food used for commercials, TV shows, and movies is real. That’s out of necessity: If an actor needs to hold ice cream for a commercial, for example, it would melt after the first take. Fake food is created by first making a mold of the actual food to be depicted. Rubber or foam is put into the mold and shaped to size. The most important and difficult parts are sculpting and painting the details of the actual food item onto the rubber or foam.
Money
While only 8% of the world’s currency is physical money, creating the mold for it is still a large operation. U.S. note currency, made from cotton and linen, and hand-drawn, can take years to design before being approved. Engravers, who train for 12 to 15 years, make exact copies on steel plates that will be used as molds for approved designs. The finished plate is soaked in a nickel and salt solution for about 22 hours. During that time, an electrical current causes an identical plate to grow on top of the existing one.
Ripped jeans
Each part of the jean is cut out individually from denim and then sewn together before going through a rigorous washing routine. Next comes the fun part: distressing the jeans to create the iconic, ripped-jeans look. That process varies, but may include shooting the denim with shotgun pellets, attacking it with power tools, or sanding the material down.
Nail polish
To make nail polish, a chemist first mixes each hue from scratch using a variety of pigments. A suspension base is added next to even out the color, along with an adhesive polymer so the polish stays on the nail. Lastly, the polish is pumped into the mini-glass containers. Fun fact: the nail polish company Orly makes more than 5 tons of nail polish every day.
Lipstick
After liquid solvents are combined with a special powder and added to pigments, the mixture has to bake for hours to mix with wax so the concoction solidifies properly in a mold. When dry, workers take the lipstick from the molds without ever touching it and insert it into packaging.
Foosball tables
Most of the creation of this leisure game is done by hand. Workers saw the wood used as the support system, paint each player in the game, and even install the aluminum goal nets and scoring units to the table.
Harmonicas
The harmonica starts out as an ordinary block of wood until a cutting machine cuts chambers into both sides, called the comb. Reeds are inserted into a plate, which a tuning specialist checks using a nail file to sand down any reed that isn’t tuned perfectly. Then, the reed plate is put on top of the comb, a cover is sandwiched on both sides, and a mouthpiece is added.
Aluminum foil
The process of creating this popular foil involves the process of repeatedly thinning out a large block of aluminum. First, a huge block of pure aluminum is melted in a natural gas furnace for three to eight hours. After it is solidified, the block—which is more than 14 feet tall and weighs more than 16,000 pounds—is put through high-pressure machines to crush and thin the material until it goes from almost 18 inches to just two-tenths of an inch thick.
Metal snap bracelets
What lies inside these childhood bracelets may surprise you. Some—more often than not the cheaper kind—are made from recycled tape measures with a fabric cover placed over it.
Rope
To make rope, fibers are squeezed together to create three bundles. These are then attached to a wheeled machine sent from one end of the factory to the other, more than 1,000 feet away. This is done in order to stretch and tighten the rope into twists and is known as the rope walk.
Honey
A beekeeper extracts honey from beehives by first spraying the hive with smoke in order to disrupt the bees’ “alarm pheromone,” which they use to warn each other of danger. The smoke also initiates the bees’ “house on fire” response, which is to go into the hive and start eating up all the honey so they can take it with them. Slowed by food and not sharing panic warnings, they’ll be more docile for the honey extraction. The hive consists of removable wooden frames so the beekeeper can easily remove the honeycomb and brush the bees off each frame, blow them off with an air compressor or leaf blower, or install “escapes” that allow a bee to exit but not come back in. At the factory, frames are spun in a machine to extract all of the honey from the cells.
Popcorn
Kernels at the factory are put into a machine that vibrates and has powerful pans, causing the grain to float on air. The kernels that don’t do this are discarded. A half-pound of kernels is then tested at 446 degrees Fahrenheit. To pass the test, the kernels must expand 44.5 and a half times their original volume.
Matches
The first step to making matches involves combining gelatin capsules with other chemicals to create a binder for the match head compound. This takes 40 minutes. Then, a machine dips numerous splints into the mixture for five seconds to create the match.
Candy canes
After this holiday treat's mixture of corn syrup and other ingredients is created and stretched, the 100-pound block of red and white strips is put through machines to thin out the concoction. At this point in the process, the sugar mixture is loose and bendable, and moves through the conveyor belt in a wave-like fashion while being twisted into rope. Lastly, the cane is cooled and hardened.