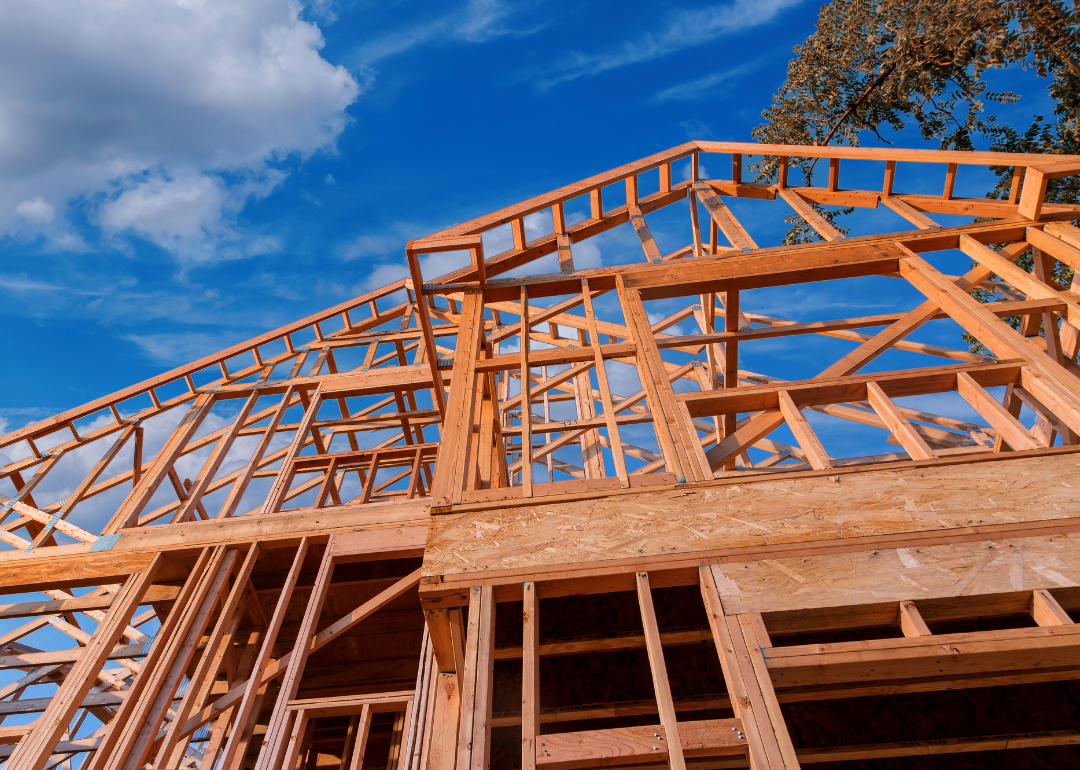
How prices for 5 major homebuilding materials have changed during COVID-19
This story originally appeared on Stacker and was produced and distributed in partnership with Stacker Studio.
How prices for 5 major homebuilding materials have changed during COVID-19
The perennial desire for more living space, investors diving into the home-rental business, and the surge in remote work during the coronavirus pandemic, have contributed to a soaring rate of home renovations and booming housing market. Add in the Federal Reserve lowering mortgage rates, which reached a record-low 30-year fixed rate of 2.72% in 2020, and you’ve got a buying bonanza in a seller’s market.
But not every aspect of the housing market is cheaper now than it was a year ago. In fact, the prices of many raw materials shot up significantly during the pandemic, whether from supply-chain gaps, wildfires out West, or peeled-back production to meet cratered demand that has yet to recalibrate. As homeowners flocked to hardware stores seeking supplies last spring, building supply chains couldn’t keep up. The price increases for materials, in some cases in the double digits, put home renovations and new builds out of reach for many—or at least deprioritized until costs fall.
UpNest analyzed the Federal Reserve's Economic Data (FRED) database to discover just how much prices for homebuilding materials have changed during COVID-19. Commodity data from January to March 2020 and 2021 was used to calculate the one-year change from January through April of 2020 and 2021. FRED data is based on the Producer Price Index (PPI), an indexed dataset derived from a sample of more than 25,000 establishments, providing approximately 100,000 price quotations. The PPI considers commodity pricing by comparing the price of a given date to the price during an index year. For example, if the index year is 1984, the price at a given date is based on the commodity’s price being set at $100 in 1984.
Keep reading to see how some of the most common homebuilding materials have spiked in the last year.
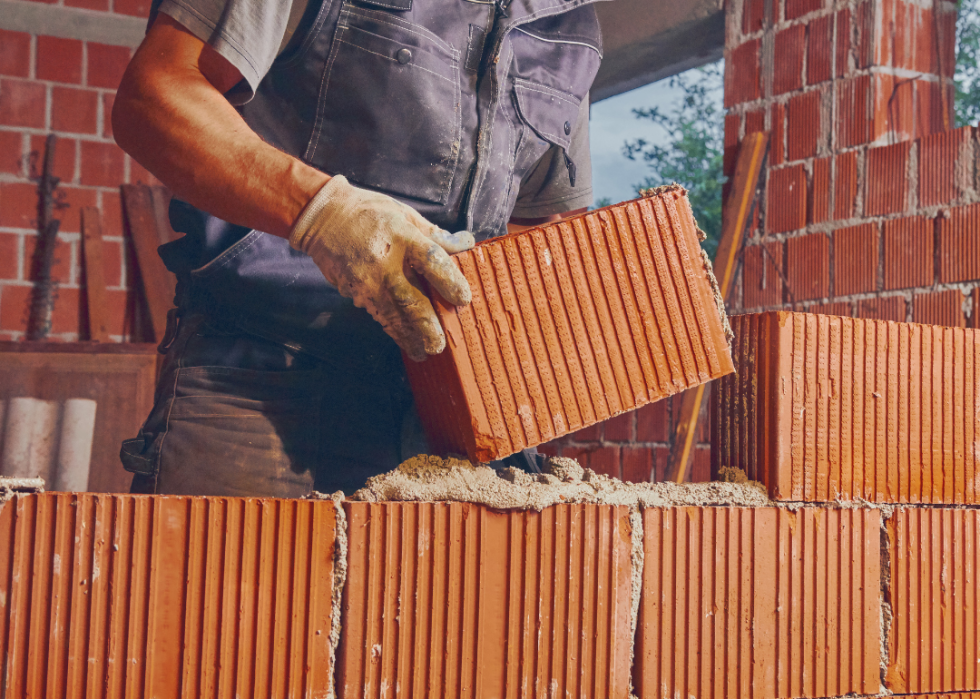
Bricks and blocks
- Building or Common Brick:
--- Price increase during COVID-19: 3.5%
--- Jan. 2020 to April 2020 index score: 200.5
--- Jan. 2021 to April 2021 index score: 207.6
- Indexed year: 1984
Building homes out of brick has been going out of vogue for decades, dating back to post-World War II construction that sought to stand apart from urban architecture and instead incorporate contemporary building codes allowing for a variety of materials for residential construction. Bricks in the 21st century are mostly used as decorative flourishes for walkways, accent walls, or exterior veneers. Today’s biggest brick manufacturer in the U.S., Acme Brick, makes $750.8 million in annual revenue; the country’s biggest lumber producer, Weyerhauser, has an annual revenue of more than $7 billion.
Required shutdowns of plants and holes in getting materials from manufacturer to distribution to sale squeezed the brick industry, driving up costs from end to end along the supply chain at the same time demand went through the roof with people updating their homes and building new.
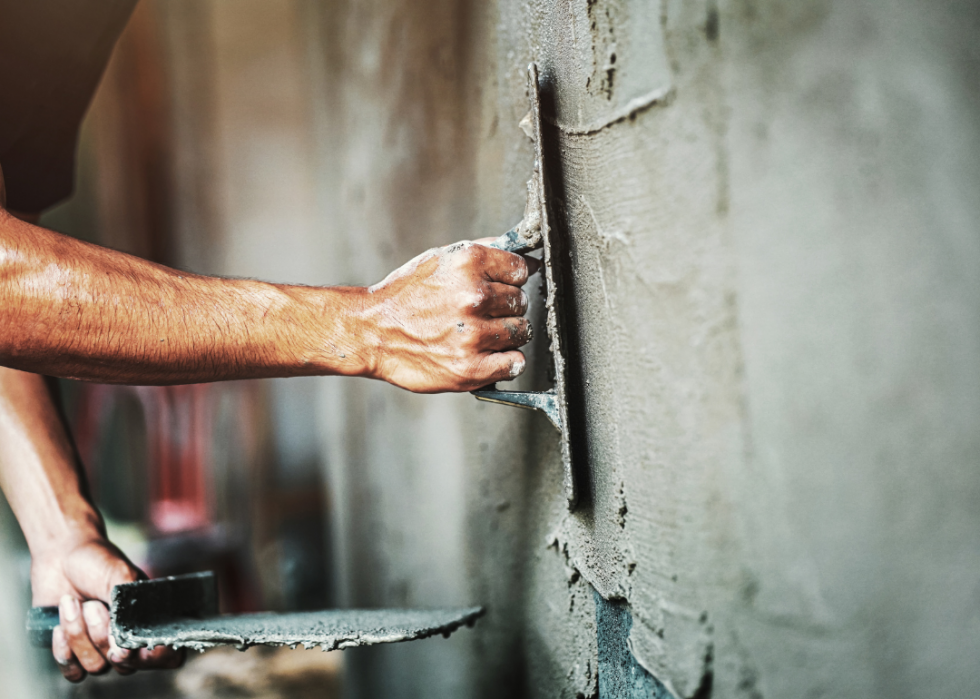
Cement
- Concrete Ingredients and Related Products:
--- Price increase during COVID-19: 3.6%
--- Jan. 2020 to April 2020 index score: 316.3
--- Jan. 2021 to April 2021 index score: 327.8
- Cement, Hydraulic:
- Price increase during COVID-19: 3.0%
--- Jan. 2020 to April 2020 index score: 257.8
--- Jan. 2021 to April 2021 index score: 265.5
- Indexed year: 1982
One of the most important raw building materials in home and commercial projects is concrete. Limestone, the raw material from which concrete is made, is abundant, meaning price increases are rarely related to shortages (as they are with other materials on this list). Instead, increased demand created by the recent housing boom is the primary culprit behind climbing costs. Additionally, new trade policy, specifically tariffs imposed on concrete imports from Japan, has pushed costs up even higher.

Glass
- Glass:
--- Price increase during COVID-19: 2.4%
--- Jan. 2020 to April 2020 index score: 150.7
--- Jan. 2021 to April 2021 index score: 154.4
- Indexed year: 1982
Even before the pandemic hit, a glass shortage already existed, edging prices higher bit by bit. A year and a half in, and that raw materials shortage has only grown, driving prices further up. Additionally, glass-making is a difficult process that involves keeping furnaces running continually; when stay-at-home orders shut down production lines it also created backups that forced customers to wait for months to have their orders filled. These two factors account for the price increase, and indicate that builders would be better off using less glass (especially in places like front doors that could do without it) for the next year or so.
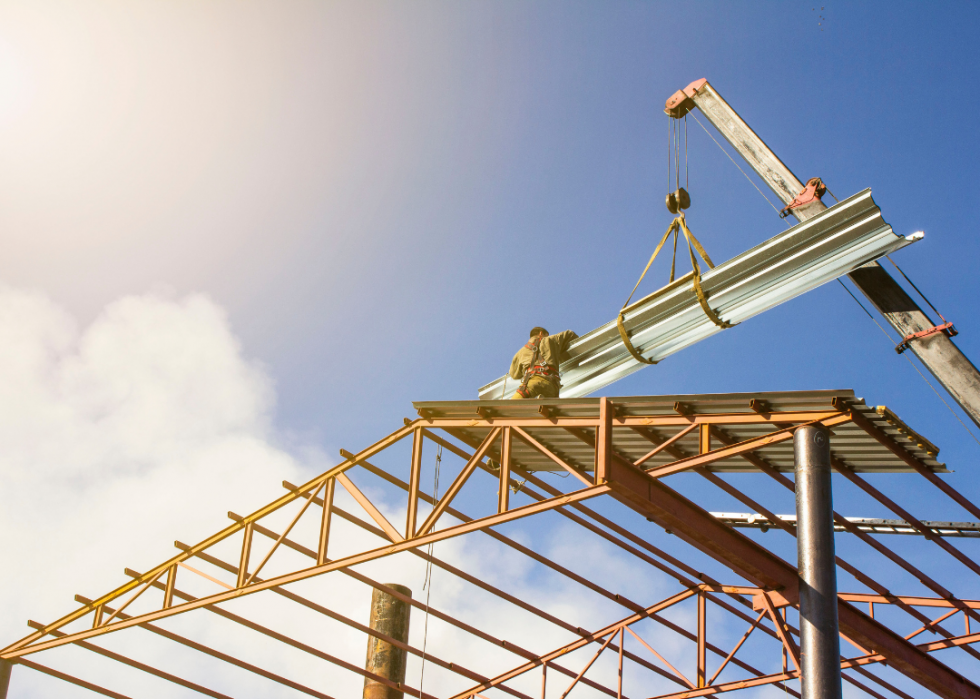
Steel
- Steel Wire, Stainless Steel:
--- Price increase during COVID-19: 0.1%
--- Jan. 2020 to April 2020 index score: 118.4
--- Jan. 2021 to April 2021 index score: 118.5
- Steel Pipe and Tube, Stainless Steel:
- Price increase during COVID-19: 6.4%
--- Jan. 2020 to April 2020 index score: 101.3
--- Jan. 2021 to April 2021 index score: 107.8
- Indexed year: 2010
In November 2019, steel prices hit an all-time low as the economy slowed private and commercial new builds. By January 2020, they had more than rebounded, and steel manufacturers increased prices across the board. Companies that gave an explanation for the jump, like Nucor Corp. and NLMK, cited extending lead times and strong order placement as the housing market boomed. An S&P Global Platts poll released in April 2021 found that U.S. steel producers expect prices to remain at all-time highs for the next six months or so.
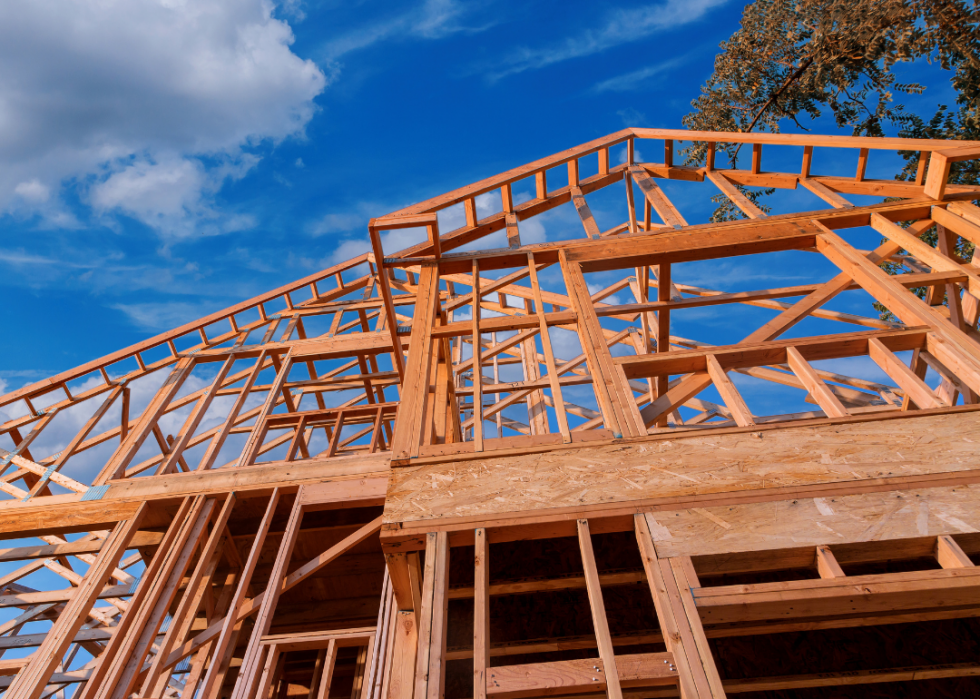
Wood
- Hardwood lumber:
--- Price increase during COVID-19: 19.6%
--- Jan. 2020 to April 2020 index score: 203.2
--- Jan. 2021 to April 2021 index score: 242.9
- Softwood lumber:
- Price increase during COVID-19: 78.8%
--- Jan. 2020 to April 2020 index score: 230.5
--- Jan. 2021 to April 2021 index score: 412.2
- Indexed year: 1982
Wood has seen a larger price increase than any other homebuilding material over the last year. There are multiple reasons for this jump, according to the National Association of Home Builders, including mill closures and an uptick in DIY projects. At the start of the pandemic, many mills were closed by stay-at-home orders—which obviously cut production—while also leading them to believe that housing would be adversely affected and demand for lumber would go down. Contrary to their predictions, the housing market has boomed, which has only increased demand for hardwood and softwood. This increase, coupled with growing sales at big-box retailers for DIY projects, has sent prices skyrocketing.
The supply shortage and heightened cost of wood and other building materials throughout the pandemic has delayed construction projects, while also driving up the price of building a home. While the outlook regarding building materials for the remainder of 2021 and beyond is still fairly unknown, research group Capital Economics expects that the demand and the price of lumber, for example, will drastically drop once 2022 comes to a close.
This story was produced and distributed in partnership with Stacker Studio.