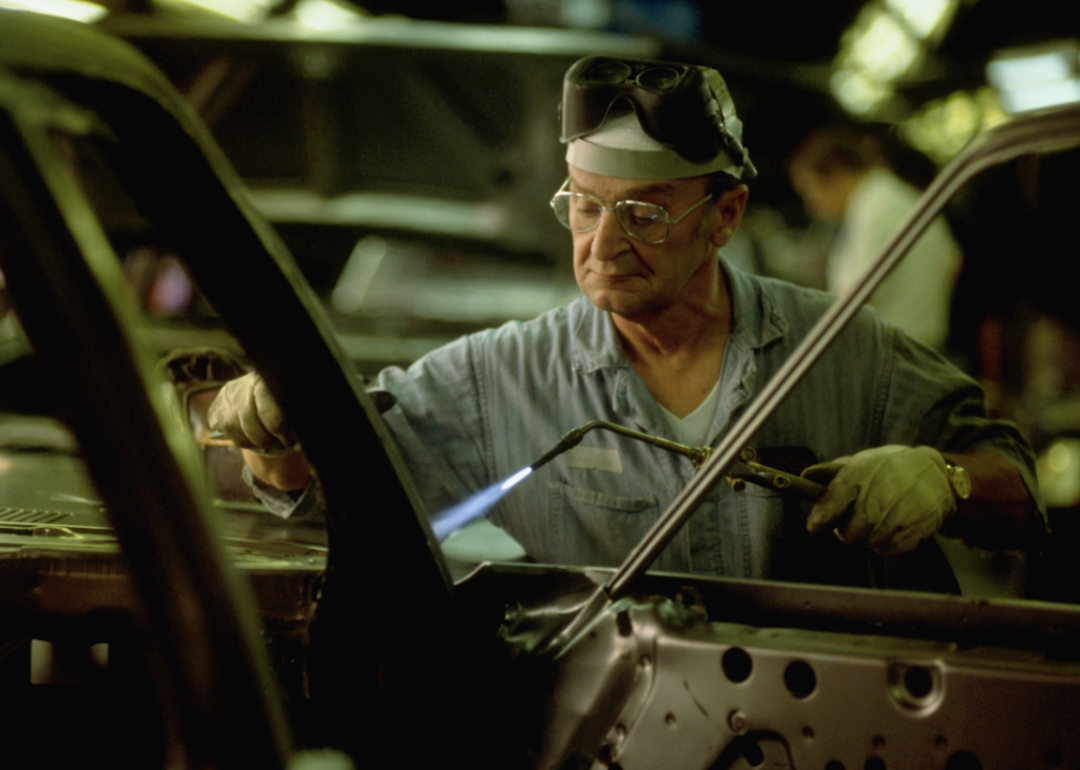
Manufacturing history from the year you were born
Manufacturing history from the year you were born
Between the mid-to-late 18th century and early-to-mid 19th century, economies in what would come to be called industrialized nations made a dramatic shift from hand production to machine production during the Industrial Revolution. In much of the world, however, modern manufacturing truly came into its own in the 20th century, and the United States of America led the charge—at least at first.
More than any other sector, manufacturing produced the American middle class and established the United States as a global superpower with the highest standard of living in history. By the 1920s and '30s, about 20% of the U.S. workforce labored in the manufacturing sector. Those laborers didn't only make toasters, roller skates, transistors, and Barbie dolls. The country's factories also formed the backbone of its military might—America's enemies learned the hard way that, when needed, the U.S. Armed Forces could rely on the country's manufacturers to produce supplies and armaments in quantities so massive that no enemy could possibly withstand the onslaught.
American manufacturers developed astonishing innovations in everything from automobiles and household goods to computers and communications. They changed the way electricity is transmitted, how people talk to each other, and how products were packaged. Some of their greatest technological advances were improvements in how their own factories operated and produced goods—and some of the greatest manufacturers in history were lost forever along the way.
Stacker compiled a year-by-year list of manufacturing history over the course of a century from a variety of sources, including historic St. Louis Fed data on employees since 1939, hourly earnings since 1939, average hours since 1939, and manufacturing production since 1920. Stacker also used inflation data from the Minneapolis Fed and historical GDP (since 1947) data from the Bureau of Economic Analysis.
The following is a synopsis of how manufacturing evolved during—and steered the evolution of—an American century defined by advances so revolutionary that their impact is still being felt today.
1920
- Manufacturing output index: 5.2 (+3.2% compared to previous year)
The year 1920 kicked off one of the greatest and longest periods of economic expansion in American history as the United States emerged from World War I as the world’s manufacturer. With most of Europe in ruins, the victorious and unscathed United States would produce almost half of everything the world made as the American economy grew by an astonishing 42% in the decade leading up to the Depression. The aviation and auto industries came of age in the 1920s, electricity went mainstream in homes and factories, mass-production entered the modern era, and an insatiable demand for new and exciting consumer goods of all kinds became the norm.
1921
- Manufacturing output index: 4 (-23.7% compared to previous year)
Established in 1921, the Workers Educational Bureau (WEB) signaled the start of organized vocational education in the United States. American universities started adopting labor extension programs and manufacturing began its modern partnership with academia.
1922
- Manufacturing output index: 5.2 (+30.2% compared to previous year)
In 1922, a group of scientists and academics created the company that would become Raytheon Technologies. Originally focused on refrigeration and electronics, it would grow to become one of the biggest aerospace and defense manufacturers in the world with 40,000 patents, 195,000 employees, $74 billion in annual sales, and an $8 billion research-and-development department. It remains one of the most enduring symbols of the powerful partnership between the U.S. government and private-sector manufacturing.
1923
- Manufacturing output index: 6.1 (+17.3% compared to previous year)
Founded in 1908, General Motors came of age when Alfred Sloan took over as president in 1923—he would later serve as chairman of the board through the 1950s. Sloan restructured the company to focus on five main automotive divisions: Chevrolet, Oldsmobile, Pontiac, Buick, and Cadillac. Under Sloan’s stewardship, GM became one of Detroit’s famed “Big Three” automakers and one of the greatest manufacturing companies in history.
1924
- Manufacturing output index: 5.7 (-6.3% compared to previous year)
The Toyota Motor Company can be traced to 1924, when Sakichi Toyoda invented the Toyoda Model G Automatic Loom. The most efficient and productive loom in the world, it was based on the concept of "jidoka," which describes an automated process that stops right away when a problem is detected so that a human supervisor can intervene. The advance allowed one human to supervise as many as 50 looms, and jidoka became a key principle in the Toyota Production System (TPS), and later, lean manufacturing.
1925
- Manufacturing output index: 6.4 (+11.8% compared to previous year)
On June 6, 1925, Walter P. Chrysler formed the Chrysler Corporation from the struggling Maxwell Motor Company. It would join GM and Ford to form the greatest triumvirate in American manufacturing history. Michigan would remain the heart of the auto manufacturing world for generations.
1926
- Manufacturing output index: 6.7 (+5.1% compared to previous year)
By 1926, Buick had combined all its operations under one roof, even manufacturing the bolts, nuts, and screws that would be used to fasten its vehicles together in-house. That year in Flint, Michigan, its engineers unveiled a revolutionary new system called the “unified assembly line.” The world’s largest and most efficient car assembly system, it used overhead conveyors to ferry components and supplies from all over the facility and provided a model for modern automation.
1927
- Manufacturing output index: 6.7 (-0.5% compared to previous year)
The year 1927 marked the end of one glorious American manufacturing era and the beginning of another. That year, Ford stopped production of the car that started it all, the venerable Model T, after 18 years and 15 million cars. At the same time, Ford unveiled the Model A, a far more advanced and highly customizable vehicle—customers snapped up 4.8 million of them by the time the Model A’s production run ended in 1932.
1928
- Manufacturing output index: 7.1 (+5.6% compared to previous year)
When it opened in 1928, the Ford River Rouge Complex in Dearborn, Michigan—known informally as “the Rouge”—was the largest integrated factory on the planet. It represented near-total manufacturing self-sufficiency, with Ford in control of the coal mines, rubber plantations, iron mines, and forests that provided raw materials to the thousands of suppliers that served the Rouge. One year later in 1929, the Rouge employed more than 100,000 people.
1929
- Manufacturing output index: 7.8 (+10.6% compared to previous year)
The Roaring '20s came to a screeching halt when the stock market crashed starting on Thursday, Oct. 24, 1929. Manufacturing output would plummet for several consecutive years to come. Jobs dried up and the recently unemployed bought fewer goods, which reduced output and evaporated jobs even further in an endless cycle that swept all industries into the Great Depression.
1930
- Manufacturing output index: 6.4 (-18.3% compared to previous year)
By 1930, three years before the Toyota automotive division was spun off from Toyoda Automatic Loom Works in 1933, the company produced “The Toyota Way.” The operating manual, which outlined the principles of the Toyota Production System (TPS), presented a blueprint for a slimmed-down, and highly responsive manufacturing philosophy that would come to be known as lean manufacturing. Its principles are still in widespread use today.
1931
- Manufacturing output index: 5.2 (-18.1% compared to previous year)
While unemployment was in double-digits worldwide by 1931, New Yorkers needed only to look up to see the greatest testament to American manufacturing ever built—the Empire State Building. One year after the Chrysler Building immortalized one of the country’s great manufacturers, the Empire State Building was completed as the grandest skyscraper ever built. Soaring 1,250 feet toward the heavens, it contained 10 million bricks, 200,000 cubic feet of Indiana limestone, 730 tons of aluminum, and 60,000 tons of American-manufactured steel.
1932
- Manufacturing output index: 4 (-22.9% compared to previous year)
Franklin Delano Roosevelt won the presidency in a landslide election just as the unemployment rate crawled toward its 1933 peak of nearly 25%. Although things were bad everywhere, manufacturing took an especially hard hit. While unemployment was around 20% nationwide in 1933, it was more like 30% in areas that depended on heavy industry—tens of thousands of desperate Americans were now living in the cars they used to build.
1933
- Manufacturing output index: 4.8 (+19.5% compared to previous year)
In 1933, President Franklin Roosevelt chose longtime progressive workers rights advocate Frances Perkins to be his secretary of labor. Perkins, whose reforms improved the lives of countless manufacturing workers, was the first woman ever to serve in the U.S. Cabinet and the longest-serving secretary of labor in history.
1934
- Manufacturing output index: 5.3 (+8.9% compared to previous year)
In the mid-1930s, pharmaceutical manufacturing began taking on its modern form as scientists discovered things like vitamins and learned more about hormones and body chemistry. Pharmaceutical chemists and the manufacturers who turned their ideas into products began standardizing their drugs and treatments for mass production.
1935
- Manufacturing output index: 6.2 (+17.8% compared to previous year)
In 1935, John L. Lewis of the United Mine Workers formed the Committee for Industrial Organizations (CIO), a federation of unions that represented industrial workers in the United States and Canada in industries like auto manufacturing, rubber, and steel production. Three years later in 1938, it became the Congress of Industrial Organizations, the largest collective bargaining organization for manufacturing workers in the world. Open to African Americans and fiercely loyal to President Roosevelt, the CIO was the chief rival—and later chief partner—of the older American Federation of Labor (AFL).
1936
- Manufacturing output index: 7.4 (+19.3% compared to previous year)
By 1936, GM was America’s most dominant auto manufacturer by far—a position it often achieved at the expense of its workers. For 44 days between 1936-37, the United Auto Workers (UAW) fought back by staging a sit-in—instead of picketing, they simply showed up to work at the GM factor in Flint, sat down, refused to work, and refused to leave. After much resistance, GM eventually gave into worker demands and the strike remains one of the most decisive victories in the history of the labor movement.
1937
- Manufacturing output index: 8.1 (+9.2% compared to previous year)
1937 saw great leaps forward in the development and manufacturing of plastics, which by then were pushing new boundaries in military manufacturing. Invented two years earlier in 1935 as synthetic silk, nylon was being used in the production of body armor, parachutes, and ropes while Plexiglas was replacing heavy, breakable glass aircraft windows. Plastic production in the United States would go on to grow by 300% during World War II.
1938
- Manufacturing output index: 6.2 (-23.2% compared to previous year)
When President Franklin Roosevelt signed the Fair Labor Standards Act (FLSA) in 1938, it wasn’t just manufacturing workers who benefited from child labor laws, the minimum wage, and the 40-hour workweek, but factory work had changed forever—and for the better. The landmark legislation was a before-and-after moment for the American worker and remains the bedrock of federal labor law today.
1939
- Manufacturing output index: 7.3 (+18.8% compared to previous year)
- Manufacturing employees: 9.5 million
- Average manufacturing hourly wages inflation adjusted: $9.09
- Average manufacturing hours worked: 37.7
In 1939, RCA's National Broadcasting Company (NBC) stunned the world with the first television broadcast at the 1939 New York World's Fair. The moment foreshadowed a manufacturing bonanza. In 1950, fewer than one in 10 U.S. households owned a television, but by the end of the 1970s, there was a set in 98% of American homes.
1940
- Manufacturing output index: 8.7 (+18.2% compared to previous year)
- Manufacturing employees: 10.1 million (+6.9%)
- Average manufacturing hourly wages inflation adjusted: $9.63 (+6%)
- Average manufacturing hours worked: 38.2 (+1.1%)
In 1940, the Ford, Willys, and Bantam companies partnered to design a quick and capable 4x4 utility vehicle to accommodate America’s modern and mobile military. In just 75 days, they designed the Willys Quad, a prototype of what they called a “jeep.” It would become one of the most enduring symbols of World War II and of the manufacturing muscle that propped up America’s military might.
1941
- Manufacturing output index: 11.1 (+27.8% compared to previous year)
- Manufacturing employees: 12.1 million (+20.1%)
- Average manufacturing hourly wages inflation adjusted: $10.54 (+9.4%)
- Average manufacturing hours worked: 40.7 (+6.7%)
There’s a common misconception that Pearl Harbor flipped some kind of a switch that transformed American manufacturing from a civilian private-sector endeavor to an arm of the U.S. military overnight, but the truth is that private industry was already heavily invested in war production. FDR put GM’s president William Knudsen in charge of all U.S. military production in 1940—he swapped one of America’s best-paying executive positions for a $1 government salary. In 1941, months before the attacks, Henry Ford’s son Edsel Ford and Ford legend Charlie Sorensen drafted plans to build a factory that could produce one B-24 Liberator—America’s deadliest bomber—every hour.
1942
- Manufacturing output index: 12.9 (+16.7% compared to previous year)
- Manufacturing employees: 14 million (+15.8%)
- Average manufacturing hourly wages inflation adjusted: $11.60 (+10%)
- Average manufacturing hours worked: 43.2 (+6%)
In 1941 alone, America’s automakers produced 3 million cars, but from January 1942 through the end of World War II, they made only 139 more vehicles combined. One month after Pearl Harbor, President Roosevelt created the War Production Board and directed it to convert America’s peacetime industries into the greatest military-production machine the world had ever seen. Nazi Germany, fascist Italy, Imperial Japan, and their proxies would now face not only 16 million American service members, but a manufacturing goliath operating from unbombed cities that could churn out planes, tanks, guns, and shells, seemingly into infinity.
1943
- Manufacturing output index: 16.1 (+24.5% compared to previous year)
- Manufacturing employees: 16.2 million (+15.1%)
- Average manufacturing hourly wages inflation adjusted: $12.66 (+9.2%)
- Average manufacturing hours worked: 45.2 (+4.6%)
Factory workers had to install hundreds of thousands of rivets to produce a single bomber during World War II, and women were often chosen as riveters because they were more likely to fit in the tight spaces inside of airplane bodies. Norman Rockwell’s famous 1943 “Rosie the Riveter” cover of the Saturday Evening Post embodied the spirit of the millions of women who worked long hours in ordnance factories to support the effort. Rosie was actually an amalgamation of several women, including Rose Bonavita, who drove a record-setting 3,300 rivets in a single six-hour shift, and Rose Will Monroe, who left the B-24 assembly line to do military promotional films in Hollywood.
1944
- Manufacturing output index: 17.4 (+8.1% compared to previous year)
- Manufacturing employees: 15.9 million (-1.6%)
- Average manufacturing hourly wages inflation adjusted: $13.25 (+4.6%)
- Average manufacturing hours worked: 45.4 (+0.5%)
By 1944, America's home front manufacturing efforts had smothered the enemy with endless equipment, machines, arms, and supplies of every stripe—and the country's automakers had become the airplane factory for democracy. Before the war, only three companies manufactured engines for military aircraft, but Studebaker, Packard, Ford, Dodge, Chevrolet, and Buick were quick to learn the craft. Together, they made 799,000 airplane propellers and 808,000 aircraft engines and by 1945, yearly manufacturing output had grown tenfold.
1945
- Manufacturing output index: 14.5 (-16.7% compared to previous year)
- Manufacturing employees: 14.3 million (-10.4%)
- Average manufacturing hourly wages inflation adjusted: $12.76 (-3.7%)
- Average manufacturing hours worked: 43.4 (-4.2%)
1945 signaled the beginning of the greatest economic and manufacturing boom in American history. The War Production Board was dissolved and more than 10 million service members returned home to enter the workforce in a newly wealthy country. The postwar boom era, however, was not without its growing pains.
1946
- Manufacturing output index: 12.1 (-16.8% compared to previous year)
- Manufacturing employees: 13.5 million (-5.3%)
- Average manufacturing hourly wages inflation adjusted: $12.41 (-2.7%)
- Average manufacturing hours worked: 40.4 (-7.1%)
During the war, millions of union laborers kept their grievances mostly to themselves or to their labor leaders as the government struck bargains with union bosses to prevent strikes and other work disruptions. When the war ended, however, so did the bargains, and manufacturing workers and other laborers participated in the largest and most widespread strikes in U.S. history: the 1945-46 Strike Wave.
1947
- Manufacturing output index: 13.5 (+11.6% compared to previous year)
- Manufacturing percent of GDP: 39.2%
- Manufacturing employees: 14.3 million (+5.7%)
- Average manufacturing hourly wages inflation adjusted: $12.54 (+1%)
- Average manufacturing hours worked: 40.4 (+0.1%)
Although Motorola technicians wouldn’t place the first cellular phone call until 1973, the prototype for that phone was created by Bell Labs in 1947. Called the DynaTAC, it was originally developed for use in police cars. It didn’t exactly kick off a manufacturing boom right away, but 60 years later in 2007, a company called Apple would revolutionize global manufacturing and mobile technology with a very distant relative of DynaTAC: the iPhone.
1948
- Manufacturing output index: 14 (+3.8% compared to previous year)
- Manufacturing percent of GDP: 37.2%
- Manufacturing employees: 14.3 million (+0.3%)
- Average manufacturing hourly wages inflation adjusted: $12.85 (+2.5%)
- Average manufacturing hours worked: 40.1 (-0.8%)
In 1948, the McDonald brothers, Richard and Maurice, opened their first self-serve, limited-menu burger stand in San Bernardino, California. Soon, businessman Ray Kroc would join the team, expand the McDonald’s franchising operations, and eventually take over. The business model he created would create a new type of assembly line work that would eventually employ millions of laborers who manufactured meals in the new fast-food industry.
1949
- Manufacturing output index: 13.2 (-5.5% compared to previous year)
- Manufacturing percent of GDP: 37.4%
- Manufacturing employees: 13.3 million (-7.2%)
- Average manufacturing hourly wages inflation adjusted: $13.46 (+4.7%)
- Average manufacturing hours worked: 39.2 (-2.3%)
The post-war boom started in earnest in 1949 and manufacturing soared to meet the demand—and the demand seemed bottomless. Americans bought 6.2 million cars that year as 10 million televisions were being watched in American homes. The TV boom was about to take off for real as RCA that year developed a workable format for color television.
1950
- Manufacturing output index: 15.4 (+16.5% compared to previous year)
- Manufacturing percent of GDP: 38.9%
- Manufacturing employees: 14 million (+5.5%)
- Average manufacturing hourly wages inflation adjusted: $13.96 (+3.7%)
- Average manufacturing hours worked: 40.5 (+3.3%)
Many Americans first heard of the Defense Production Act when President Trump invoked it in response to supply shortages related to the coronavirus pandemic, but it’s actually a Korean War-era law signed by Harry Truman in 1950. With the War Production Board gone, the Defense Production Act gave the federal government the authority to, among other things, compel private manufacturing companies to meet the needs of the military during times of crisis.
1951
- Manufacturing output index: 16.6 (+8% compared to previous year)
- Manufacturing percent of GDP: 38.7%
- Manufacturing employees: 15.1 million (+7.5%)
- Average manufacturing hourly wages inflation adjusted: $14.23 (+1.9%)
- Average manufacturing hours worked: 40.7 (+0.5%)
One of the most consequential companies in American manufacturing history was incorporated in 1951: Texas Instruments. TI would be instrumental in developing game-changing technologies like silicon transistors and integrated circuits, which in the near future would transform everything from computers to ballistic missiles. TI created some of the most transformative and most mass-produced products in the world, like the first transistor radio and the first pocket calculator.
1952
- Manufacturing output index: 17.3 (+4% compared to previous year)
- Manufacturing percent of GDP: 37.3%
- Manufacturing employees: 15.3 million (+1.5%)
- Average manufacturing hourly wages inflation adjusted: $14.68 (+3.1%)
- Average manufacturing hours worked: 40.8 (+0.1%)
Just as the Defense Production Act was compelling American manufacturers to shift their peacetime efforts toward military production once again, this time for the Korean War, the United Steelworkers of America launched a massive strike against U.S. Steel and other industry giants. In a dramatic private sector vs. government showdown, President Harry Truman nationalized the steel industry through an executive order to secure supplies for the war. In a historic ruling, the Supreme Court ruled that the president did not have the authority to seize control of the steel industry.
1953
- Manufacturing output index: 18.9 (+9% compared to previous year)
- Manufacturing percent of GDP: 38.4%
- Manufacturing employees: 16.1 million (+5.5%)
- Average manufacturing hourly wages inflation adjusted: $15.55 (+6%)
- Average manufacturing hours worked: 40.6 (-0.4%)
Ten years after the first general-purpose computer was developed in 1943, engineers learned how to generate graphics using mathematical equations, which allowed them to create computer numerical control (CNC) machines that could manipulate physical tools. It was the beginning of computer-aided design (CAD) and computer-aided manufacturing (CAM), which would revolutionize production in all industries in the coming decades.
1954
- Manufacturing output index: 17.6 (-6.8% compared to previous year)
- Manufacturing percent of GDP: 37.5%
- Manufacturing employees: 15 million (-7%)
- Average manufacturing hourly wages inflation adjusted: $15.80 (+1.6%)
- Average manufacturing hours worked: 39.8 (-2.1%)
Scientists at Bell Labs developed the first working electrical transistor—one of the most important inventions in history—in 1947. In 1954, however, engineers at Texas Instruments changed the semiconductor material from germanium to silicon, which offered far superior operating characteristics, and created what is today the central component of nearly all modern microchips. Electronics—and electronics manufacturing—had entered the silicon age.
1955
- Manufacturing output index: 19.9 (+13.1% compared to previous year)
- Manufacturing percent of GDP: 38.2%
- Manufacturing employees: 15.5 million (+3.5%)
- Average manufacturing hourly wages inflation adjusted: $16.60 (+5.1%)
- Average manufacturing hours worked: 40.8 (+2.6%)
In 1955, years of in-house labor rivalries were put to rest with the merger of the American Federation of Labor (AFL), which represented craft unions, and the Congress of Industrial Organizations (CIO), which represented manufacturers and other industry workers. The AFL-CIO remains the largest confederacy of labor unions in America. Also that year, the polio vaccine changed medicine and pharmaceutical manufacturing forever—polio was eradicated in the United States less than 25 years later.
1956
- Manufacturing output index: 20.6 (+3.8% compared to previous year)
- Manufacturing percent of GDP: 37.8%
- Manufacturing employees: 15.9 million (+2.2%)
- Average manufacturing hourly wages inflation adjusted: $17.28 (+4.1%)
- Average manufacturing hours worked: 40.5 (-0.7%)
Computers were still cartoonishly large in 1956 and offered few practical benefits for the manufacturing sector, but that would quickly change—and manufacturers would soon be churning out mountains of computers themselves. Part of that transition can be traced to 1956, when IBM released the 305 RAMAC, the world’s first hard drive. The mechanical dinosaur was the size of a refrigerator and weighed one ton and—astonishingly, it still works.
1957
- Manufacturing output index: 20.9 (+1.3% compared to previous year)
- Manufacturing percent of GDP: 37.1%
- Manufacturing employees: 15.8 million (-0.4%)
- Average manufacturing hourly wages inflation adjusted: $17.57 (+1.7%)
- Average manufacturing hours worked: 39.9 (-1.5%)
In 1957, Toyota Motor Sales, U.S.A., Inc., was formed and opened its new U.S. headquarters in Hollywood, California. The next year, the very first Japanese car ever sold in the United States—a Toyota Toyopet sedan—changed hands in what had been a former Rambler dealership.
1958
- Manufacturing output index: 19.4 (-7% compared to previous year)
- Manufacturing percent of GDP: 36.7%
- Manufacturing employees: 14.7 million (-7.2%)
- Average manufacturing hourly wages inflation adjusted: $17.57 (+0%)
- Average manufacturing hours worked: 39.3 (-1.6%)
In 1958, scientists from Bell Labs invented the first optical laser. Lasers are now used in manufacturing across a range of industries, including computer, auto, and clothing manufacturing. They can deliver intense cutting power, precision welding capabilities, and they can drill, solder, melt, and mark materials.
1959
- Manufacturing output index: 21.9 (+12.5% compared to previous year)
- Manufacturing percent of GDP: 37.9%
- Manufacturing employees: 15.3 million (+4.6%)
- Average manufacturing hourly wages inflation adjusted: $18.17 (+3.4%)
- Average manufacturing hours worked: 40.3 (+2.8%)
Industrial automation took a giant—two tons, to be exact—leap forward when George Devol and Joseph Engelberger developed the world's first industrial robot. It was given instructions through a magnetic drum and carried out those instructions using hydraulic actuators. Its movements were accurate to within 1/10,000 of an inch.
1960
- Manufacturing output index: 22.3 (+2.2% compared to previous year)
- Manufacturing percent of GDP: 37.5%
- Manufacturing employees: 15.4 million (+0.7%)
- Average manufacturing hourly wages inflation adjusted: $18.54 (+2%)
- Average manufacturing hours worked: 39.8 (-1.4%)
The arrival of transistors spelled certain death for the big, slow, hot, and bulky vacuum tubes that came before. Tiny, powerful, and almost infinitely versatile, transistors were still expensive to manufacture. In 1960, IBM changed all that when it developed the first fully automated transistor assembly line, which could produce and test 1,800 individual transistors every single hour.
1961
- Manufacturing output index: 22.4 (+0.3% compared to previous year)
- Manufacturing percent of GDP: 36.5%
- Manufacturing employees: 15 million (-2.8%)
- Average manufacturing hourly wages inflation adjusted: $18.80 (+1.4%)
- Average manufacturing hours worked: 39.9 (+0.2%)
In 1961, GM installed the world’s first industrial robot, a Unimate, at its Ternstedt plant in Trenton, New Jersey. Alongside its human counterparts, this new worker—which never had to eat, sleep, use the bathroom, or take a personal day—used a 4,000-pound arm to stack molten hot die-cast metal with precision and ease.
1962
- Manufacturing output index: 24.4 (+8.8% compared to previous year)
- Manufacturing percent of GDP: 36.7%
- Manufacturing employees: 15.5 million (+3.2%)
- Average manufacturing hourly wages inflation adjusted: $19.17 (+2%)
- Average manufacturing hours worked: 40.4 (+1.4%)
On July 2, 1962, retail shopping in the United States changed forever when Sam Walton opened his first Walmart store in Rogers, Arkansas. The Walmart revolution would create hundreds of thousands of mostly low-paying retail jobs at the expense of similar numbers of high-paying manufacturing jobs. Walmart changed the nature of buyer-producer relationships as the company relied on cheap Chinese imports produced by overseas manufacturers that Walton infamously squeezed to manufacture high volumes of goods at the lowest cost possible.
1963
- Manufacturing output index: 25.9 (+6.3% compared to previous year)
- Manufacturing percent of GDP: 36.4%
- Manufacturing employees: 15.6 million (+0.9%)
- Average manufacturing hourly wages inflation adjusted: $19.55 (+2%)
- Average manufacturing hours worked: 40.6 (+0.4%)
In 1963, the Equal Pay Act outlawed wage discrimination based on gender. By 1970, nearly one in three manufacturing workers—about 29%—were women. A half-century later, that percentage remains almost identical.
1964
- Manufacturing output index: 27.7 (+6.9% compared to previous year)
- Manufacturing percent of GDP: 36.3%
- Manufacturing employees: 15.9 million (+1.6%)
- Average manufacturing hourly wages inflation adjusted: $19.85 (+1.5%)
- Average manufacturing hours worked: 40.8 (+0.5%)
One of the biggest breakthroughs for industrial robots came in 1964 when GM outfitted its massive plant in Lordstown, Ohio, with 66 Unimates. The first true assembly line robots, they would do more than 90% of body welding for GM by the end of the decade instead of 20%–40% of automated welding at traditional plants.
1965
- Manufacturing output index: 30.7 (+10.7% compared to previous year)
- Manufacturing percent of GDP: 36.6%
- Manufacturing employees: 16.6 million (+4.6%)
- Average manufacturing hourly wages inflation adjusted: $20.23 (+1.9%)
- Average manufacturing hours worked: 41.2 (+1.1%)
In 1965, consumer advocate Ralph Nader published “Unsafe at Any Speed,” a scathing indictment of the automobile industry’s reluctance to spend money to make cars safer. The bestselling book galvanized a nation already shocked by a staggering rise in auto fatalities. Automobile manufacturing would never be the same again.
1966
- Manufacturing output index: 33.5 (+9.2% compared to previous year)
- Manufacturing percent of GDP: 36.7%
- Manufacturing employees: 17.7 million (+6.4%)
- Average manufacturing hourly wages inflation adjusted: $20.44 (+1%)
- Average manufacturing hours worked: 41.4 (+0.4%)
Public outcry and government response to “Unsafe at Any Speed” was immediate, and in 1966, President Lydon Johnson signed the Highway Safety Act and the National Traffic and Motor Vehicle Safety Act. The legislation authorized the government to require automakers to design, test, and manufacture vehicles to meet certain safety standards and include specific safety equipment, like seat belts.
1967
- Manufacturing output index: 34.1 (+1.9% compared to previous year)
- Manufacturing percent of GDP: 35.9%
- Manufacturing employees: 17.9 million (+1.2%)
- Average manufacturing hourly wages inflation adjusted: $20.72 (+1.4%)
- Average manufacturing hours worked: 40.6 (-2%)
In the 1960s, a Japanese citizen named Seiichi Nakajima developed the Total Productive Maintenance (TPM) system, which was designed to help manufacturers improve operations by making the most efficient use of manufacturing machines. Out of TPM came the concept of Overall Equipment Effectiveness (OEE), which is today considered the gold standard for measuring manufacturing productivity. OEE measures what a manufacturer could have made if all the operation’s machines were working at peak efficiency.
1968
- Manufacturing output index: 36 (+5.6% compared to previous year)
- Manufacturing percent of GDP: 35.7%
- Manufacturing employees: 18.2 million (+1.8%)
- Average manufacturing hourly wages inflation adjusted: $21.21 (+2.4%)
- Average manufacturing hours worked: 40.8 (+0.5%)
In 1968, the UAW—by that time the International Union, United Automobile, Aerospace and Agricultural Implement Workers of America—split from the AFL-CIO and formed the Alliance for Labor Action. Huge numbers of manufacturing workers were now separated from the largest federation of labor unions in the United States. Also that year, Charles Sorensen, the iconic Ford production chief credited with pioneering the first moving assembly line in 1913, died.
1969
- Manufacturing output index: 37.6 (+4.4% compared to previous year)
- Manufacturing percent of GDP: 35.2%
- Manufacturing employees: 18.6 million (+2%)
- Average manufacturing hourly wages inflation adjusted: $21.39 (+0.8%)
- Average manufacturing hours worked: 40.7 (-0.3%)
On Oct. 9, 1969, something happened that should be impossible—the Rouge River near the Ford plant in Michigan caught fire. Far from impossible, actually, it was the third major river in two years to burst into flames near a large American manufacturing center, most famously, the Cuyahoga River fire in Cleveland. The moment sparked national outrage against what the public saw as greedy industrialists destroying the natural environment by polluting for profit—the Environmental Protection Agency (EPA) was created the next year.
1970
- Manufacturing output index: 35.9 (-4.5% compared to previous year)
- Manufacturing percent of GDP: 33.3%
- Manufacturing employees: 17.8 million (-3.9%)
- Average manufacturing hourly wages inflation adjusted: $21.31 (-0.4%)
- Average manufacturing hours worked: 39.8 (-2%)
1970 was a year of major reform in the manufacturing industry. Not only was the Environmental Protection Agency formed to regulate things like pollution and emissions, but that same year, Congress passed the Occupational Safety and Health Act. OSHA protects workers in virtually all industries against things like extreme cold and heat, mechanical injuries, exposure to toxins, falls, electrocution, and the many other hazards that maimed and killed generations of manufacturing laborers before.
1971
- Manufacturing output index: 36.5 (+1.5% compared to previous year)
- Manufacturing percent of GDP: 32.7%
- Manufacturing employees: 17.2 million (-3.8%)
- Average manufacturing hourly wages inflation adjusted: $21.78 (+2.2%)
- Average manufacturing hours worked: 39.9 (+0.2%)
In 1971, Federal Express was founded in Little Rock, Arkansas. The company’s groundbreaking real-time package-tracking system, which has now been adopted industrywide, revolutionized the supply chain and logistics operations that manufacturers around the world rely on to succeed.
1972
- Manufacturing output index: 40.3 (+10.4% compared to previous year)
- Manufacturing percent of GDP: 32.9%
- Manufacturing employees: 17.7 million (+2.9%)
- Average manufacturing hourly wages inflation adjusted: $22.62 (+3.9%)
- Average manufacturing hours worked: 40.5 (+1.6%)
In 1972, the Coalition of Black Trade Unionists was formed to represent African American members of more than three dozen unions, many of whom were women. The CBTU became a powerful force not just in labor, but in politics, civil rights, and global human rights—it was the first American labor organization to pass resolutions against Apartheid South Africa.
1973
- Manufacturing output index: 43.9 (+9% compared to previous year)
- Manufacturing percent of GDP: 33.8%
- Manufacturing employees: 18.6 million (+5.2%)
- Average manufacturing hourly wages inflation adjusted: $22.85 (+1%)
- Average manufacturing hours worked: 40.7 (+0.4%)
By 1973, the power and potential of integrated circuits was no secret, but manufacturing them in quantity was costly, time-consuming, and inexact. Then Texas Instruments—which originally developed the integrated circuit, or microchip—created ABACUS II, which finally made the automated assembly of integrated circuits possible and practical. Those mass-produced integrated circuits would be the life force of the coming revolution in computers and computer-driven manufacturing.
1974
- Manufacturing output index: 43.8 (-0.2% compared to previous year)
- Manufacturing percent of GDP: 34.9%
- Manufacturing employees: 18.5 million (-0.4%)
- Average manufacturing hourly wages inflation adjusted: $22.35 (-2.2%)
- Average manufacturing hours worked: 40 (-1.6%)
In 1974, the Volvo Kalmar Assembly Plant in Sweden revolutionized the traditional assembly line with the introduction of automated guided vehicles (AGVs). Instead of car bodies moving down a fixed line, AGVs were independent moving platforms that shuttled individual car bodies between stations. Built for both manufacturing efficiency and worker comfort and safety, the battery-powered platforms moved and swiveled into the optimal position for each task.
1975
- Manufacturing output index: 39.2 (-10.6% compared to previous year)
- Manufacturing percent of GDP: 33.6%
- Manufacturing employees: 16.9 million (-8.6%)
- Average manufacturing hourly wages inflation adjusted: $22.35 (+0%)
- Average manufacturing hours worked: 39.4 (-1.5%)
For most Americans in 1975, typewriters still ruled the day as they had for generations, but Bill Gates and Paul Allen dreamed of changing all that when they established Microsoft. The software company, which would soon embark on a historic partnership with IBM to build the computers of the future, made billionaires out of both of them and took computer manufacturing from a niche industry to a new global force.
1976
- Manufacturing output index: 42.7 (+9% compared to previous year)
- Manufacturing percent of GDP: 33.9%
- Manufacturing employees: 17.5 million (+3.7%)
- Average manufacturing hourly wages inflation adjusted: $22.88 (+2.4%)
- Average manufacturing hours worked: 40.1 (+1.8%)
In 1976, college dropouts Steve Jobs and Steve Wozniak formed Apple Computers and introduced the Apple I. The company would go on to become one of the driving forces of the new economy and earn its place as one of the most important manufacturing companies in American history.
1977
- Manufacturing output index: 46.4 (+8.6% compared to previous year)
- Manufacturing percent of GDP: 34.2%
- Manufacturing employees: 18.2 million (+3.6%)
- Average manufacturing hourly wages inflation adjusted: $23.41 (+2.3%)
- Average manufacturing hours worked: 40.3 (+0.5%)
Although it didn’t ban U.S. customary units of measurement, the Metric Conversion Act of 1975 declared the metric system to be America’s preferred system of weights and measures. It was the result of a yearslong campaign to get the United States on board with the rest of the industrialized world as the global economy pulled more of humanity into its orbit. By the late 1970s, companies like Black & Decker, IBM, John Deere, Procter & Gamble, and Xerox were in some stage of metrication.
1978
- Manufacturing output index: 49.2 (+6.1% compared to previous year)
- Manufacturing percent of GDP: 34%
- Manufacturing employees: 18.9 million (+4.2%)
- Average manufacturing hourly wages inflation adjusted: $23.71 (+1.2%)
- Average manufacturing hours worked: 40.4 (+0.1%)
In 1978, Unimation developed the Programmable Universal Machine for Assembly (PUMA) with support from GM. An advanced robotic arm, PUMA is still in use today.
1979: Peak
- Manufacturing output index: 50.7 (+3.1% compared to previous year)
- Manufacturing percent of GDP: 34.2%
- Manufacturing employees: 19.4 million (+2.6%)
- Average manufacturing hourly wages inflation adjusted: $23.15 (-2.4%)
- Average manufacturing hours worked: 40.2 (-0.5%)
Manufacturing in the United States had its finest hour in 1979 when 19.4 million Americans earned their wages in the sector. Despite steep population increases, about 8 million of those jobs would be gone by 2010.
1980
- Manufacturing output index: 48.9 (-3.6% compared to previous year)
- Manufacturing percent of GDP: 33.1%
- Manufacturing employees: 18.7 million (-3.6%)
- Average manufacturing hourly wages inflation adjusted: $22.19 (-4.1%)
- Average manufacturing hours worked: 39.7 (-1.2%)
The year 1980 witnessed a great acceleration of the trend toward miniaturization, which was made possible by transistors, integrated circuits, and other milestone inventions in previous decades. The year before in 1979, Sony unveiled the Walkman and manufacturers across the world were churning out fax machines, video game consoles, camcorders, and consumer electronics of all stripes that got better, smaller, and cheaper with each release. Also that year, 3M—one of America’s greatest manufacturers—debuted something that office workers, teachers, parents, and humans in general immediately wondered how they had ever lived without: Post-It Notes.
1981
- Manufacturing output index: 49.4 (+1% compared to previous year)
- Manufacturing percent of GDP: 32.7%
- Manufacturing employees: 18.6 million (-0.5%)
- Average manufacturing hourly wages inflation adjusted: $22.13 (-0.3%)
- Average manufacturing hours worked: 39.8 (+0.3%)
Most of today’s personal computers trace their ancestry to Aug. 12, 1981, when IBM introduced the IBM 5150, or IBM PC. The primary driver of the PC revolution, tens of thousands, then hundreds of thousands, then millions of the machines were in homes, schools, and businesses across the country. Not only did it launch a new era of computer mass-production manufacturing, but manufacturers themselves used PCs to help run their operations.
1982
- Manufacturing output index: 46.7 (-5.5% compared to previous year)
- Manufacturing percent of GDP: 30.9%
- Manufacturing employees: 17.4 million (-6.8%)
- Average manufacturing hourly wages inflation adjusted: $22.16 (+0.1%)
- Average manufacturing hours worked: 39 (-2.2%)
In 1982, the Singer company stopped production at its historic plant in Elizabeth, New Jersey, which at one point employed tens of thousands of people on its assembly lines and recruited star athletes from nearby schools to work at Singer and play for its legendary baseball team. It was, like so many other former manufacturing giants, the victim of decreased product interest and intense overseas competition, mostly from Asia. Also that year, Honda opened the first Japanese auto plant on American soil in Marysville, Ohio—instead of importing cars to the United States, the Japanese were now making them here.
1983
- Manufacturing output index: 49 (+4.8% compared to previous year)
- Manufacturing percent of GDP: 30.2%
- Manufacturing employees: 17 million (-1.8%)
- Average manufacturing hourly wages inflation adjusted: $22.31 (+0.7%)
- Average manufacturing hours worked: 40.1 (+2.9%)
In 1983, Schwinn closed its famed Chicago plant, laying off 1,800 workers, and from then on mostly distributed bikes built in places like Taiwan under the Schwinn name. It was a blow not just to the iconic bike maker, but to the city of Chicago and American manufacturing in general. In 1899, four years after Arnold, Schwinn & Co. was founded in 1895, more than half of the bicycles manufactured in the United States came from Chicago.
1984
- Manufacturing output index: 53.7 (+9.8% compared to previous year)
- Manufacturing percent of GDP: 30.1%
- Manufacturing employees: 17.9 million (+5.1%)
- Average manufacturing hourly wages inflation adjusted: $22.27 (-0.2%)
- Average manufacturing hours worked: 40.6 (+1.4%)
By 1984, the computer age was evolving at a blinding pace. Apple introduced the Macintosh computer that year, complete with features like a mouse and graphical user interface. Michael Dell formed the Dell Computer Corporation and inventions like the CD-ROM, flash memory, the IBM 3480 cartridge tape system all emerged in 1984, the same year the term "cyberspace" was coined. Computer manufacturing was now one of the most exciting, most profitable, and fastest-growing industries in history.
1985
- Manufacturing output index: 54.6 (+1.6% compared to previous year)
- Manufacturing percent of GDP: 28.7%
- Manufacturing employees: 17.8 million (-0.6%)
- Average manufacturing hourly wages inflation adjusted: $22.33 (+0.3%)
- Average manufacturing hours worked: 40.5 (-0.3%)
Dell’s meteoric rise to an incredible $25 billion in sales by 2020 began in 1985. That year, the nascent computer company implemented imaginative changes in manufacturing and the supply chain when it began producing built-to-order computers. In the age of automated mass production, Dell was offering custom manufacturing to the masses.
1986
- Manufacturing output index: 55.8 (+2.2% compared to previous year)
- Manufacturing percent of GDP: 27.5%
- Manufacturing employees: 17.6 million (-1.5%)
- Average manufacturing hourly wages inflation adjusted: $22.38 (+0.2%)
- Average manufacturing hours worked: 40.7 (+0.4%)
A lighthearted comedy on the surface, Ron Howard’s 1986 movie “Gung Ho,” starring Michael Keaton, explored the very serious apprehensions many Americans were having about the decline of U.S. manufacturing. That decline coincided with the rise of Japan, whose streamlined companies seemed to make everything faster, better, smaller, and cheaper than their American counterparts by the mid-1980s. The film portrayed Keaton as a labor leader managing a culture clash after his American auto plant is taken over by a Japanese corporation.
1987
- Manufacturing output index: 59 (+5.7% compared to previous year)
- Manufacturing percent of GDP: 27.7%
- Manufacturing employees: 17.6 million (+0.3%)
- Average manufacturing hourly wages inflation adjusted: $21.99 (-1.8%)
- Average manufacturing hours worked: 41 (+0.7%)
In 1987, Motorola executive Bill Smith created a quality and process improvement strategy called Six Sigma, which strived for nearly 100% defect-free production. Witnessing Motorola’s rapid success with the strategy, other major companies would soon follow suit.
1988
- Manufacturing output index: 62.1 (+5.3% compared to previous year)
- Manufacturing percent of GDP: 27.9%
- Manufacturing employees: 17.9 million (+1.7%)
- Average manufacturing hourly wages inflation adjusted: $21.72 (-1.2%)
- Average manufacturing hours worked: 41 (+0.2%)
John Krafcik—who served in CEO positions at Google, Hyundai, and Waymo—is credited with coining the term “lean manufacturing” in an article in the Fall 1988 issue of MIT Sloan Management Review. He described a bold process that involved keeping only the bare minimum inventory on hand to make it easier to identify and solve problems. The daring idea, which took measured risks in the pursuit of efficiency, can be traced to the philosophy first outlined in “The Toyota Way” in 1930.
1989
- Manufacturing output index: 62.6 (+0.8% compared to previous year)
- Manufacturing percent of GDP: 27.6%
- Manufacturing employees: 18 million (+0.4%)
- Average manufacturing hourly wages inflation adjusted: $21.34 (-1.7%)
- Average manufacturing hours worked: 40.9 (-0.3%)
In 1989, Masaki Fujihata used stereolithography to create a representation of fruit using 3D printing. That same year, engineers and scientists developed fused deposition modeling (FDM), which—unlike virtually all manufacturing that came before—created forms and shapes by adding material instead of by removing it, like virtually all manufacturing that came before.
1990
- Manufacturing output index: 63.1 (+0.8% compared to previous year)
- Manufacturing percent of GDP: 26.7%
- Manufacturing employees: 17.7 million (-1.6%)
- Average manufacturing hourly wages inflation adjusted: $21.07 (-1.3%)
- Average manufacturing hours worked: 40.5 (-1%)
In 1990, Boeing launched the Model 777, its first new jetliner in more than a decade—but the plane really stood out for how it was manufactured. The 777 was the first airplane to be digitally “preassembled” on a computer. For the first time in aviation manufacturing history, an expensive, time-consuming full-scale mockup wasn’t necessary.
1991
- Manufacturing output index: 61.9 (-1.9% compared to previous year)
- Manufacturing percent of GDP: 25.9%
- Manufacturing employees: 17.1 million (-3.5%)
- Average manufacturing hourly wages inflation adjusted: $20.90 (-0.8%)
- Average manufacturing hours worked: 40.4 (-0.2%)
On Aug. 6, 1991, British computer scientist Tim Berners-Lee published the world’s first website as part of the World Wide Web program while he was stationed at a particle physics lab in Switzerland. It used hypertext to link documents that were stored on different computers, provided that those computers were connected to the Internet. For the world of manufacturing—and the world in general—it was a before-and-after moment in history.
1992
- Manufacturing output index: 64.2 (+3.7% compared to previous year)
- Manufacturing percent of GDP: 25.7%
- Manufacturing employees: 16.8 million (-1.6%)
- Average manufacturing hourly wages inflation adjusted: $20.78 (-0.5%)
- Average manufacturing hours worked: 40.8 (+1%)
The North American Free Trade Agreement (NAFTA) removed trade barriers, slashed tariffs, and encouraged intracontinental trade. A complex and controversial deal, NAFTA still has passionate defenders and detractors on both sides, and it certainly produced both winners and losers—manufacturing was among the biggest losers. Five million of the 17.7 million American manufacturing jobs that existed in 1993 would disappear in the years after NAFTA took effect in 1994.
1993
- Manufacturing output index: 66.5 (+3.6% compared to previous year)
- Manufacturing percent of GDP: 25.4%
- Manufacturing employees: 16.8 million (-0.1%)
- Average manufacturing hourly wages inflation adjusted: $20.69 (-0.4%)
- Average manufacturing hours worked: 41.2 (+0.9%)
It’s fitting that American Type Founders finally shut down operations and closed its Elizabeth, New Jersey, plant in 1993. Representing the consolidation of two dozen type founders and operating as the country’s top type foundry for nearly a century, it was responsible for fonts like Franklin Gothic, Century Schoolbook, and News Gothic. Its demise signaled the beginning of the end for print publishing, which embarked on a downward spiral that continues today as newspapers, books, magazines, and published materials in general migrate to online-only formats.
1994
- Manufacturing output index: 70.4 (+5.9% compared to previous year)
- Manufacturing percent of GDP: 25.6%
- Manufacturing employees: 17 million (+1.5%)
- Average manufacturing hourly wages inflation adjusted: $20.76 (+0.3%)
- Average manufacturing hours worked: 41.7 (+1.2%)
The year 1994 witnessed the debut of Pride At Work, a national coalition of LGBTQ+ union workers, many of whom work in manufacturing. An officially recognized constituency of the AFL-CIO, it now supports more than 20 chapters across the country. Also that year, General Electric became the first Fortune 500 company to establish a web presence with www.ge.com, and Jeff Bezos founded Amazon.
1995
- Manufacturing output index: 74 (+5.1% compared to previous year)
- Manufacturing percent of GDP: 25.9%
- Manufacturing employees: 17.2 million (+1.3%)
- Average manufacturing hourly wages inflation adjusted: $20.71 (-0.3%)
- Average manufacturing hours worked: 41.3 (-0.9%)
In 1995, the Six Sigma philosophy entered the mainstream when General Electric implemented the strategy under the stewardship of legendary manufacturing CEO Jack Welch. Five years after instituting the new quality control measures, GE reported $12 billion in savings and manufacturers across the country and the world were following suit. Also that year, the National Association of Manufacturers celebrated its centennial.
1996
- Manufacturing output index: 77.6 (+4.9% compared to previous year)
- Manufacturing percent of GDP: 25.4%
- Manufacturing employees: 17.2 million (0%)
- Average manufacturing hourly wages inflation adjusted: $20.77 (+0.3%)
- Average manufacturing hours worked: 41.3 (+0%)
The year 1996 witnessed the founding of a huge number of companies that existed not in physical storefronts or even through P.O. boxes, but online websites. Manufacturing had entered a new era where producers made products for companies that didn’t store physical inventory and that interacted with their customers only through computer screens. The dot-com bubble was inflating.
1997
- Manufacturing output index: 84.2 (+8.4% compared to previous year)
- Manufacturing percent of GDP: 25.3%
- Manufacturing employees: 17.4 million (+1.1%)
- Average manufacturing hourly wages inflation adjusted: $20.93 (+0.7%)
- Average manufacturing hours worked: 41.7 (+1%)
In 2018, the manufacturing sector added 284,000 jobs, the best showing in 20 years. The year 1997 was the last year before the post-NAFTA manufacturing decline set in and the last year that manufacturing was responsible for more than 25% of the U.S. GDP. By 2009, it would be under 20%.
1998
- Manufacturing output index: 89.8 (+6.7% compared to previous year)
- Manufacturing percent of GDP: 24.4%
- Manufacturing employees: 17.6 million (+0.8%)
- Average manufacturing hourly wages inflation adjusted: $21.10 (+0.8%)
- Average manufacturing hours worked: 41.5 (-0.6%)
In 1998, an all-American manufacturing icon joined forces with the best of Germany’s auto industry when Chrysler merged with Daimler-Benz AG to become Daimler-Chrysler AG. Chrysler would now expand into the lucrative European market and Daimler-Benz would expand its American footprint in this historic cross-continent manufacturing consolidation.
1999
- Manufacturing output index: 94.3 (+5.1% compared to previous year)
- Manufacturing percent of GDP: 23.6%
- Manufacturing employees: 17.3 million (-1.4%)
- Average manufacturing hourly wages inflation adjusted: $21.26 (+0.8%)
- Average manufacturing hours worked: 41.4 (-0.2%)
In 1999, the heavily automated manufacturing sector braced for a technological apocalypse, a code formatting glitch that would crash the world's computers when their internal settings failed to cycle from the year 1999 to 2000. From alarm systems and health care products to automobiles and the factories themselves, manufacturers across all industries scrambled to file government reports and hire consultants to deal with the fallout. The apocalypse never came, and across the sector and the world, Y2K—Year 2000—came and went with a whimper.
2000
- Manufacturing output index: 98.2 (+4.1% compared to previous year)
- Manufacturing percent of GDP: 23%
- Manufacturing employees: 17.3 million (-0.3%)
- Average manufacturing hourly wages inflation adjusted: $21.26 (0%)
- Average manufacturing hours worked: 41.2 (-0.4%)
In 2000, Toyota began selling the hybrid Prius in the United States and the world—it had been available in Japan since 1997. Other hybrids had come before, but none could come close to matching the hype or the success of the Prius, an eco-conscious status symbol and an impressive feat of engineering that shifted the country toward a gas-free future. American automakers would soon be in the battery manufacturing business.
2001
- Manufacturing output index: 94.6 (-3.7% compared to previous year)
- Manufacturing percent of GDP: 21.4%
- Manufacturing employees: 16.4 million (-4.8%)
- Average manufacturing hourly wages inflation adjusted: $21.31 (+0.2%)
- Average manufacturing hours worked: 40.4 (-2.1%)
Lionel trains had been synonymous with Christmas in America since the turn of the 20th century. In February 2001, however, while Americans were still blissfully unaware of the events that would soon define the year and the generation, Lionel announced it was closing its last remaining manufacturing facility. Also that year, Converse closed its last American Chuck Taylor plant.
2002
- Manufacturing output index: 95.1 (+0.5% compared to previous year)
- Manufacturing percent of GDP: 20.7%
- Manufacturing employees: 15.3 million (-7.2%)
- Average manufacturing hourly wages inflation adjusted: $21.73 (+2%)
- Average manufacturing hours worked: 40.5 (+0.2%)
In 2002, the all-American doll changed her citizenship. That year, Mattel closed its last U.S. factory. Barbie is now made in China.
2003
- Manufacturing output index: 96.4 (+1.3% compared to previous year)
- Manufacturing percent of GDP: 20.1%
- Manufacturing employees: 14.5 million (-4.9%)
- Average manufacturing hourly wages inflation adjusted: $21.88 (+0.7%)
- Average manufacturing hours worked: 40.4 (-0.2%)
America invaded Iraq in 2003 and, as always, U.S. manufacturers pitched in to support the war effort—and to profit from it. In total, military contractors walked away from the conflict 10 years later $138 billion richer.
2004
- Manufacturing output index: 99.4 (+3.1% compared to previous year)
- Manufacturing percent of GDP: 20.1%
- Manufacturing employees: 14.3 million (-1.3%)
- Average manufacturing hourly wages inflation adjusted: $21.85 (-0.1%)
- Average manufacturing hours worked: 40.8 (+1%)
SunCore Corporation, SunLink, and Abound Solar were just a few of the alternative, light-based energy manufacturers that popped up in 2004. The concept of transforming sunlight into usable energy had been around for decades, but by the middle of the 2000s, technology existed to envision a future where solar power fueled cars, homes, businesses, factories, and even sidewalks and streets.
2005
- Manufacturing output index: 103.4 (+4.1% compared to previous year)
- Manufacturing percent of GDP: 20.4%
- Manufacturing employees: 14.2 million (-0.6%)
- Average manufacturing hourly wages inflation adjusted: $21.67 (-0.8%)
- Average manufacturing hours worked: 40.6 (-0.4%)
The streaming video movement emerged for real when YouTube was founded in 2005. Manufacturers across the world would soon learn how to post and edit videos to inform, educate, and sell to their customers, clients, suppliers, vendors, and buyers across the world.
2006
- Manufacturing output index: 106.1 (+2.6% compared to previous year)
- Manufacturing percent of GDP: 20.4%
- Manufacturing employees: 14.2 million (-0.5%)
- Average manufacturing hourly wages inflation adjusted: $21.32 (-1.6%)
- Average manufacturing hours worked: 41.2 (+1.4%)
The year 2006 saw the release of the OPC Unified Architecture (UA) protocol. A major leap forward in the Internet of Things, secure communications were now possible between apps, devices, and data sources. Soon, manufacturers would be producing millions of devices that “talk” to other devices as part of connected smart homes and businesses.
2007
- Manufacturing output index: 109 (+2.8% compared to previous year)
- Manufacturing percent of GDP: 20.6%
- Manufacturing employees: 13.9 million (-2%)
- Average manufacturing hourly wages inflation adjusted: $21.29 (-0.1%)
- Average manufacturing hours worked: 41.2 (+0.1%)
After years of gaining ground, Toyota in 2007 passed GM as the biggest automaker in the world. Also that year, Apple released the original iPhone, which would change electronics and computer manufacturing—and the world in general—forever with the arrival of the smartphone era.
2008
- Manufacturing output index: 103.8 (-4.8% compared to previous year)
- Manufacturing percent of GDP: 20.4%
- Manufacturing employees: 13.4 million (-3.4%)
- Average manufacturing hourly wages inflation adjusted: $21.09 (-1%)
- Average manufacturing hours worked: 40.8 (-1.1%)
In 2008, the Financial Times reported on something that was once unthinkable, but by that point had become inevitable—China was set to overtake the United States in manufacturing output. China was projected to account for 17% of global manufacturing compared to 16% for the United States. A dozen years later the United States is still hovering around 16%–17% while China has established itself as the world’s manufacturing superpower, accounting for more than 28% of total manufacturing output worldwide.
2009
- Manufacturing output index: 89.5 (-13.8% compared to previous year)
- Manufacturing percent of GDP: 18.1%
- Manufacturing employees: 11.8 million (-11.6%)
- Average manufacturing hourly wages inflation adjusted: $21.75 (+3.2%)
- Average manufacturing hours worked: 39.9 (-2.3%)
Nearly 50 years after the Equal Pay Act banned gender discrimination in the workplace in 1963, President Barack Obama signed the Lilly Ledbetter Fair Pay Act in 2009. The law allows women in the workplace to sue their employers over pay discrimination.
2010
- Manufacturing output index: 94.7 (+5.8% compared to previous year)
- Manufacturing percent of GDP: 19%
- Manufacturing employees: 11.5 million (-2.7%)
- Average manufacturing hourly wages inflation adjusted: $21.82 (+0.3%)
- Average manufacturing hours worked: 41.1 (+3.2%)
By 2010, America’s transformation from a nation of makers to a nation of importers was complete. In 1960, just 8% of the goods Americans purchased were manufactured overseas. Then, 50 years later in 2010, 60% of the goods sold in the United States were produced in another country and the trade deficit was nearly $500 billion.
2011
- Manufacturing output index: 97.5 (+2.9% compared to previous year)
- Manufacturing percent of GDP: 20%
- Manufacturing employees: 11.7 million (+1.7%)
- Average manufacturing hourly wages inflation adjusted: $21.52 (-1.4%)
- Average manufacturing hours worked: 41.4 (+0.7%)
In 2011, robot manufacturing combined with pharmaceutical manufacturing when scientists used nanobots to deliver targeted medications on a molecular level inside of living beings. The next big breakthrough in manufacturing, it turns out, was actually microscopic.
2012
- Manufacturing output index: 100 (+2.6% compared to previous year)
- Manufacturing percent of GDP: 19.8%
- Manufacturing employees: 11.9 million (+1.7%)
- Average manufacturing hourly wages inflation adjusted: $21.24 (-1.3%)
- Average manufacturing hours worked: 41.6 (+0.5%)
There were more than a dozen mass shootings in 2012, most notably, the Sandy Hook Elementary School shooting in Newtown, Connecticut, which killed 26 people, including 20 6- and 7-year-old children. The carnage—which was repeated many times in years prior and since—sparked a new discussion about the 2005 Protection of Lawful Commerce in Arms Act. The law puts gun manufacturers in a class almost by themselves in giving them total immunity from lawsuits related to the dangers of their products.
2013
- Manufacturing output index: 100.9 (+0.9% compared to previous year)
- Manufacturing percent of GDP: 19.6%
- Manufacturing employees: 12 million (+0.8%)
- Average manufacturing hourly wages inflation adjusted: $21.16 (-0.3%)
- Average manufacturing hours worked: 41.8 (+0.5%)
By the early 2010s, prior advances like FDM in 1989—which made the dream of 3D printing a reality, albeit a primitive one—had evolved into the modern additive manufacturing revolution. In 2013, GE, the largest manufacturer in the world, announced that it was on the precipice of using 3D printing to make jet parts.
2014
- Manufacturing output index: 102 (+1.1% compared to previous year)
- Manufacturing percent of GDP: 19%
- Manufacturing employees: 12.2 million (+1.4%)
- Average manufacturing hourly wages inflation adjusted: $21.13 (-0.2%)
- Average manufacturing hours worked: 42 (+0.3%)
In 2014, researchers unveiled something that could soon change not just manufacturing, but the military, medicine, science, art, and just about every other thing that human beings do. The world's largest robot swarm featured 1,024 cheap, one-inch "Kilobot" robots. Acting in unison, they formed together to create complex shapes like stars and letters.
2015
- Manufacturing output index: 101.5 (-0.5% compared to previous year)
- Manufacturing percent of GDP: 17.7%
- Manufacturing employees: 12.3 million (+1.2%)
- Average manufacturing hourly wages inflation adjusted: $21.48 (+1.7%)
- Average manufacturing hours worked: 41.8 (-0.4%)
While electric vehicles are now mainstream and hybrid cars are old hat, zero-emissions hydrogen fuel cell vehicles are still relatively few and unfamiliar. Unlike regular batteries that have to be charged, fuel cells use hydrogen to generate electricity directly without an external power source. The first fuel cell vehicle, the Hyundai Tucson FCEV, debuted in 2013, and by 2015, the technology existed to allow many of Hyundai’s competitors to bring hydrogen fuel cell vehicles of their own to market.
2016
- Manufacturing output index: 100.7 (-0.8% compared to previous year)
- Manufacturing percent of GDP: 16.9%
- Manufacturing employees: 12.4 million (+0.1%)
- Average manufacturing hourly wages inflation adjusted: $21.78 (+1.4%)
- Average manufacturing hours worked: 41.9 (+0.1%)
Private manufacturers helped develop rockets and designed and produced them for the military and NASA for as long as rocket technology has existed. In 2016, however, a rocket did something no rocket had ever done before—it blasted off and returned home. That year, Elon Musk’s SpaceX corporation successfully landed the world’s first reusable rocket on a barge at sea.
2017
- Manufacturing output index: 102.7 (+2% compared to previous year)
- Manufacturing percent of GDP: 16.8%
- Manufacturing employees: 12.4 million (+0.7%)
- Average manufacturing hourly wages inflation adjusted: $21.79 (+0.1%)
- Average manufacturing hours worked: 41.9 (+0.2%)
In 2017, U.S. News and World Report covered a promising development with implications that had the potential to reshape the global manufacturing landscape. Major advances in tech, particularly artificial intelligence, were driving a wave of new investments in U.S.-based manufacturing. Thanks to “reshoring,” about three-quarters of a million manufacturing jobs returned to the U.S. from overseas between 2010–2018.
2018
- Manufacturing output index: 105 (+2.3% compared to previous year)
- Manufacturing percent of GDP: 17%
- Manufacturing employees: 12.7 million (+2%)
- Average manufacturing hourly wages inflation adjusted: $21.92 (+0.6%)
- Average manufacturing hours worked: 42.1 (+0.4%)
In 2018, President Donald Trump was delivering on his campaign promise to wage a trade war with China by wielding tariffs on manufactured imported goods as a weapon. U.S. tariff revenue shot up dramatically that year, from less than $40 billion to more than $50 billion. The next year in 2019, it vaulted to $79 billion—more than twice the tariff revenue from just two years earlier in 2017.
2019
- Manufacturing output index: 104.9 (-0.2% compared to previous year)
- Manufacturing percent of GDP: 16.6%
- Manufacturing employees: 12.8 million (+1.2%)
- Average manufacturing hourly wages inflation adjusted: $22.14 (+1%)
- Average manufacturing hours worked: 41.6 (-1.3%)
In 2019, about 12.8 million Americans were employed in manufacturing, a far cry from the sector's 1979 peak. In a single month between March and April the following year, however, that number would crater to less than 11.5 million manufacturing jobs as the coronavirus crisis forced American industry to do what it had always done in times of change—evolve and adapt.